Choosing the right fabric is foundational to any successful quilting project. While a vast array of textiles exists, quilting demands specific characteristics to ensure durability, ease of handling, and a beautiful finished product.
This guide delves into the core composition of quilting fabric. We’ll explore why certain materials are favored, understanding how their unique properties contribute to the precise piecing, stitching, and lasting quality essential for every cherished quilt.
What Is Quilting Fabric?
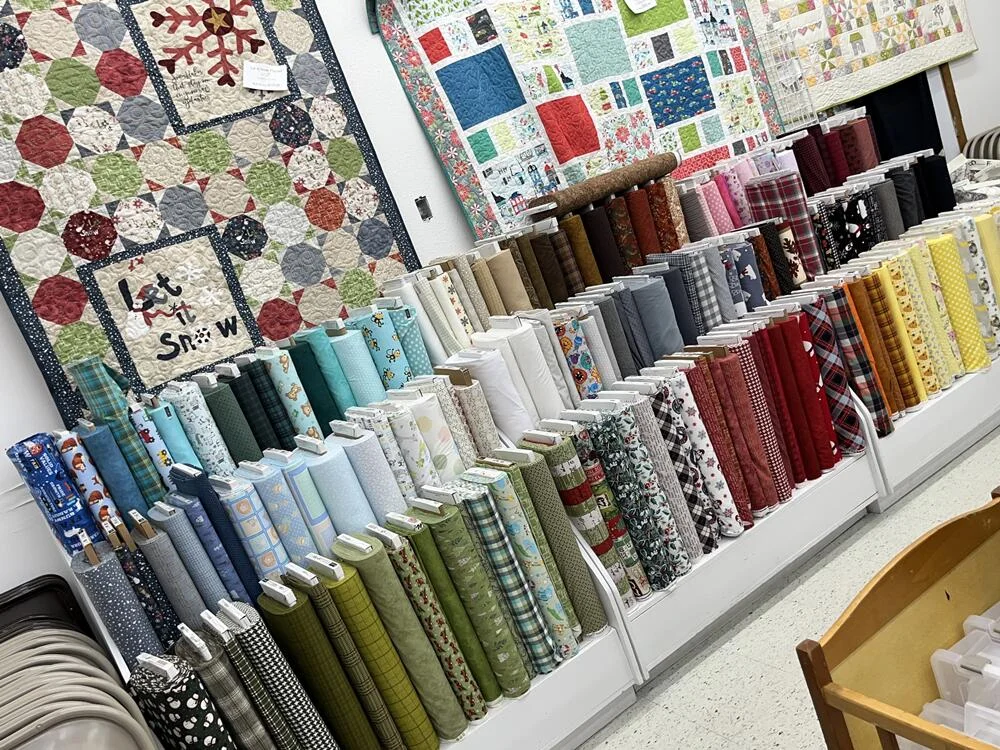
Quilting fabric, often specifically referred to as “quilting cotton,” is a type of woven textile designed with the unique demands of quilt-making in mind. It is predominantly made from 100% long-staple cotton, which gives it a smooth, durable feel and minimizes lint.
Compared to general apparel fabrics, quilting cotton typically boasts a tighter weave and a higher thread count, providing excellent stability for precise cutting and piecing of intricate designs, and reducing fraying. These characteristics ensure that the fabric holds its shape well throughout the quilting process and that the finished quilt will be resilient and maintain its beauty through years of use and washing.
What is Quilting Fabric Called?
The fabric specifically designed and used for quilting is simply called “quilting fabric.” This term refers to any fabric that is suitable for quilting projects, whether it’s 100% cotton, a cotton-polyester blend, flannel, batik, or any other type of fabric commonly used in quilting.
Quilting fabric comes in a wide variety of colors, prints, and textures, allowing quilters to choose the perfect fabric for their projects based on their preferences and the specific requirements of their designs.
What Is Quilting Fabric Made Of?
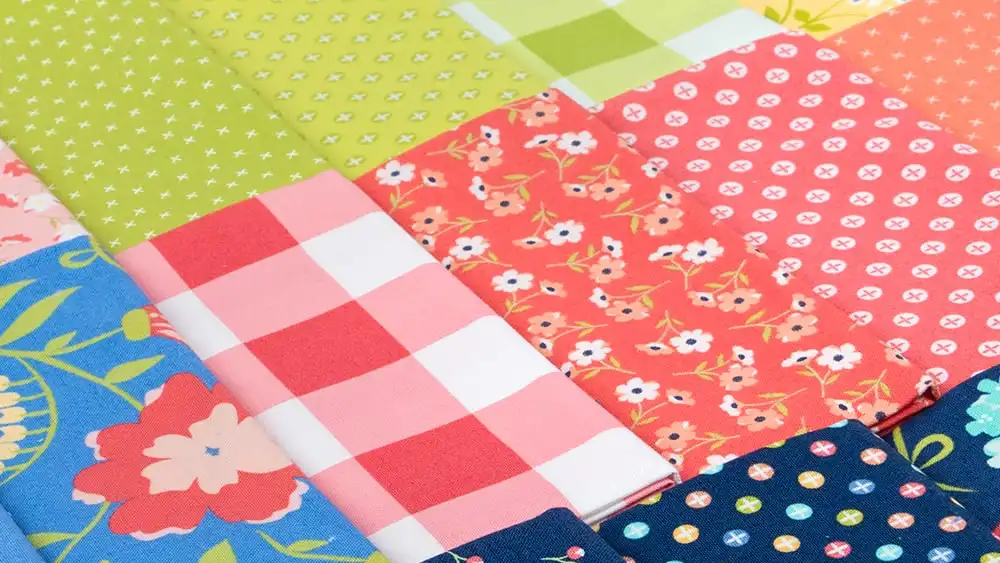
Quilting fabric’s superiority for its specific craft stems from a meticulous combination of fiber choice, yarn construction, weave density, and specialized finishing processes. It’s not merely cotton; it’s engineered cotton, designed to meet the rigorous demands of cutting intricate shapes, maintaining precise seams, and enduring decades of use and washing. Understanding these deeper technical aspects reveals why dedicated quilting cotton performs so exceptionally.
At its core, the choice of 100% long-staple cotton is paramount. “Staple” refers to the length of the individual cotton fibers; longer fibers (like those from Pima or Egyptian cotton varieties) result in stronger, smoother, and more uniform yarns when spun.
This minimizes fiber ends protruding from the yarn, leading to less lint, reduced pilling over time, and a silkier hand. From a molecular perspective, cotton is primarily cellulose, a polymer that readily absorbs water (and thus dyes) and is relatively inelastic, contributing to its dimensional stability – a critical factor for preventing distortion in quilt blocks.
The yarn construction further refines the material. High-quality quilting cotton often uses combed yarns, meaning shorter fibers and impurities have been “combed” out before spinning. This creates a smoother, stronger, and more uniform yarn compared to carded yarns. When these refined yarns are then woven, the fabric achieves a clean surface that enhances print clarity and reduces fuzziness.
The fabric construction itself, specifically the weave type and density, is crucial. Quilting fabric almost exclusively employs a plain weave (one thread over, one thread under) because it’s the strongest, most stable, and least prone to distortion. The density of this weave, often indicated by a high thread count (typically 60-75 threads per inch or more), is a key differentiator.
A higher thread count means more threads are packed into a square inch, resulting in a denser, firmer fabric. This density provides superior stability for accurate cutting, prevents excessive fraying at raw edges, and ensures seams lie flat and crisp, all essential for intricate patchwork where precision is paramount.
Finally, various finishing processes elevate raw cotton fabric to quilting fabric. Mercerization is a common chemical treatment where cotton yarns or fabric are immersed in a caustic soda solution under tension. This process permanently swells the cellulose fibers, increasing their strength, enhancing their luster, and significantly improving dye absorption and colorfastness. This means more vibrant, long-lasting colors that resist fading and bleeding.
Sanforization (or pre-shrinking) is a mechanical process that compresses the fabric to minimize residual shrinkage after washing, ensuring that different fabrics in a quilt shrink uniformly. Sizing, a temporary starch-like finish, is often applied to give the fabric body and crispness, making it easier to cut and handle, though it typically washes out in the first laundering. These combined processes ensure the fabric is not only beautiful but also resilient, stable, and easy to work with, allowing quilters to create durable, heirloom-quality pieces.
Quilting Fabric Core Distinction
While both terms are found in the textile world, it’s essential to grasp that a quilt is a finished, layered textile product, while fabric is the raw material used to create it. Imagine trying to build a house: the fabric is the lumber, bricks, and wiring, while the quilt is the completed home. This fundamental difference dictates their characteristics and uses.
Why Quilting Fabric is Unique
Quilting fabric, especially 100% long-staple cotton, is specifically engineered for the unique demands of quilt-making. Its properties are carefully controlled to ensure precision, durability, and a beautiful final product.
Superior Fiber Quality:
- 100% Long-Staple Cotton: This type of cotton uses longer individual fibers, which, when spun into yarn, results in a stronger, smoother, and more uniform thread. This significantly reduces lint production, pilling over time, and creates a more luxurious feel, essential for an heirloom-quality quilt.
- Cellulose Structure: Cotton’s natural cellulose structure allows it to absorb dyes exceptionally well, leading to vibrant, saturated colors that are less prone to fading. Its inherent inelasticity contributes to the fabric’s dimensional stability, crucial for maintaining quilt block integrity.
Precision in Yarn and Fabric Construction:
- Combed Yarns: High-quality quilting cotton often uses combed yarns, where shorter fibers and impurities are removed before spinning. This process creates a smoother, stronger yarn that results in a cleaner fabric surface, enhancing print clarity and reducing fuzziness.
- Tight Plain Weave: The fabric is almost always constructed with a plain weave (one thread over, one thread under). This simple yet robust weave is the most stable, preventing stretching and distortion during the intricate cutting and piecing phases of quilting.
- High Thread Count (60-75+ threads per inch): A higher thread count means more threads are packed into a square inch, making the fabric denser and firmer. This density provides superior stability for accurate cutting, minimizes fraying at raw edges, and ensures seams lie flat and crisp, all vital for achieving precise patchwork.
Specialized Finishing Processes:
- Mercerization: This chemical treatment involves immersing cotton in a caustic soda solution. It permanently swells the fibers, increasing strength, enhancing luster, and significantly improving dye absorption and colorfastness. This ensures that the vibrant colors of your quilt last for generations.
- Sanforization (Pre-shrinking): A mechanical process that pre-shrinks the fabric to minimize residual shrinkage after washing. This is critical for quilts, as it ensures that different fabrics within the same quilt shrink uniformly, preventing puckering and distortion after laundering.
- Sizing: A temporary starch-like finish applied to give the fabric a crisp body. This makes it easier to cut and handle precisely, especially for small pieces, though it typically washes out in the first laundering.
How is Quilting Fabric Made
Creating high-quality quilting fabric involves a series of precise manufacturing steps, transforming raw cotton fibers into the stable, vibrant material quilters rely on. This process combines traditional textile techniques with modern advancements to ensure optimal performance.
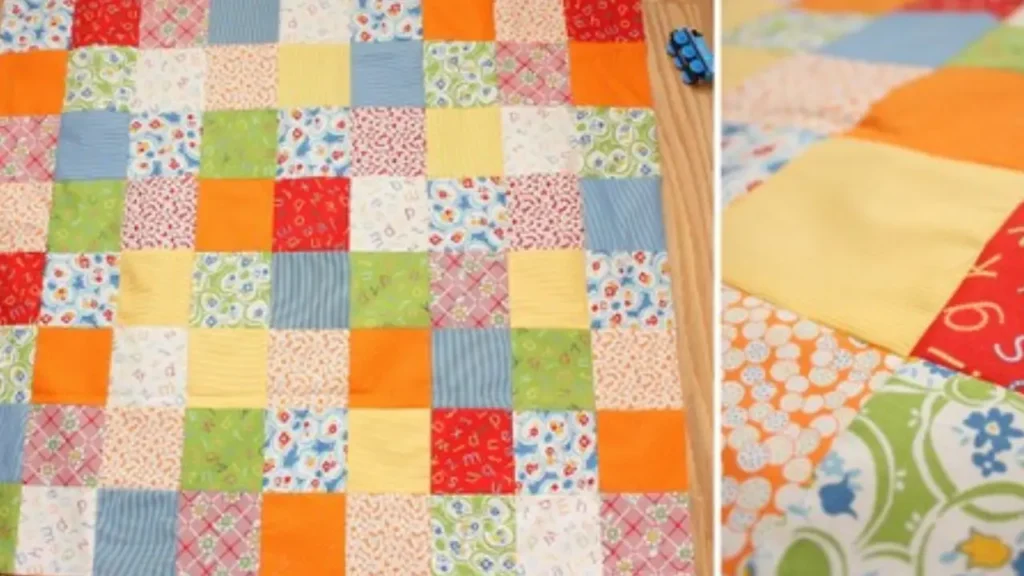
Each stage is carefully controlled to imbue the fabric with characteristics crucial for quilting, such as minimal stretch, excellent dye absorption, and resistance to fraying, making it ideal for intricate piecing and long-lasting projects.
Step 1: Fiber Preparation and Spinning
The journey begins with raw cotton fibers, which are first cleaned to remove impurities and then “carded” to align the fibers. For higher quality quilting fabric, these fibers are often further “combed” to remove shorter fibers and create a smoother, stronger cotton sliver, reducing future pilling and lint.
This prepared fiber is then spun into yarn. The quality of spinning affects the yarn’s strength and uniformity, which in turn influences the fabric’s overall durability and how consistently it absorbs dyes. A well-spun yarn is essential for the tight weave desired in quilting fabrics.
Step 2: Weaving
Once the yarn is prepared, it is woven into fabric, typically using a plain weave on industrial looms. This involves interlacing warp (longitudinal) and weft (transverse) yarns in a simple over-under pattern. The looms are set to create a very tight and dense weave.
The tight plain weave is crucial for quilting fabric as it provides exceptional dimensional stability. This minimizes stretching and distortion during the cutting and piecing stages, ensuring that intricate quilt blocks align perfectly and maintain their shape over time.
Step 3: Finishing Processes
After weaving, the raw fabric (greige goods) undergoes several finishing treatments. Mercerization is a key step, where the fabric is immersed in a caustic solution under tension. This process enhances the cotton’s strength, luster, and dramatically improves its ability to absorb dyes more vibrantly and colorfastly.
Further finishing includes sanforization (pre-shrinking) to minimize future shrinkage, ensuring different fabrics in a quilt shrink uniformly. Sizing (a temporary starch) is often applied to give the fabric crispness, making it easier to handle and cut precisely for quilters.
Step 4: Dyeing and Printing
The fabric is then dyed, often using reactive dyes that chemically bond with the cotton fibers for superior colorfastness and vibrancy. For printed fabrics, designs are applied using advanced techniques like rotary screen printing or digital printing.
These processes ensure that colors are rich, penetrate deeply, and designs are crisp and on-grain. High-quality dyeing and printing are vital for the aesthetic appeal and longevity of a quilt, preventing colors from bleeding or fading over time.
Step 5: Quality Control and Packaging
Throughout the entire manufacturing process, rigorous quality control checks are implemented. This includes inspecting for weave imperfections, dye inconsistencies, and print clarity to ensure the fabric meets specific standards for quilting.
Finally, the finished quilting fabric is rolled onto bolts, packaged, and prepared for distribution to fabric stores and quilters worldwide. This final step ensures the fabric reaches consumers in optimal condition, ready for creative use.
How To Choose The Right Quilting Fabric?
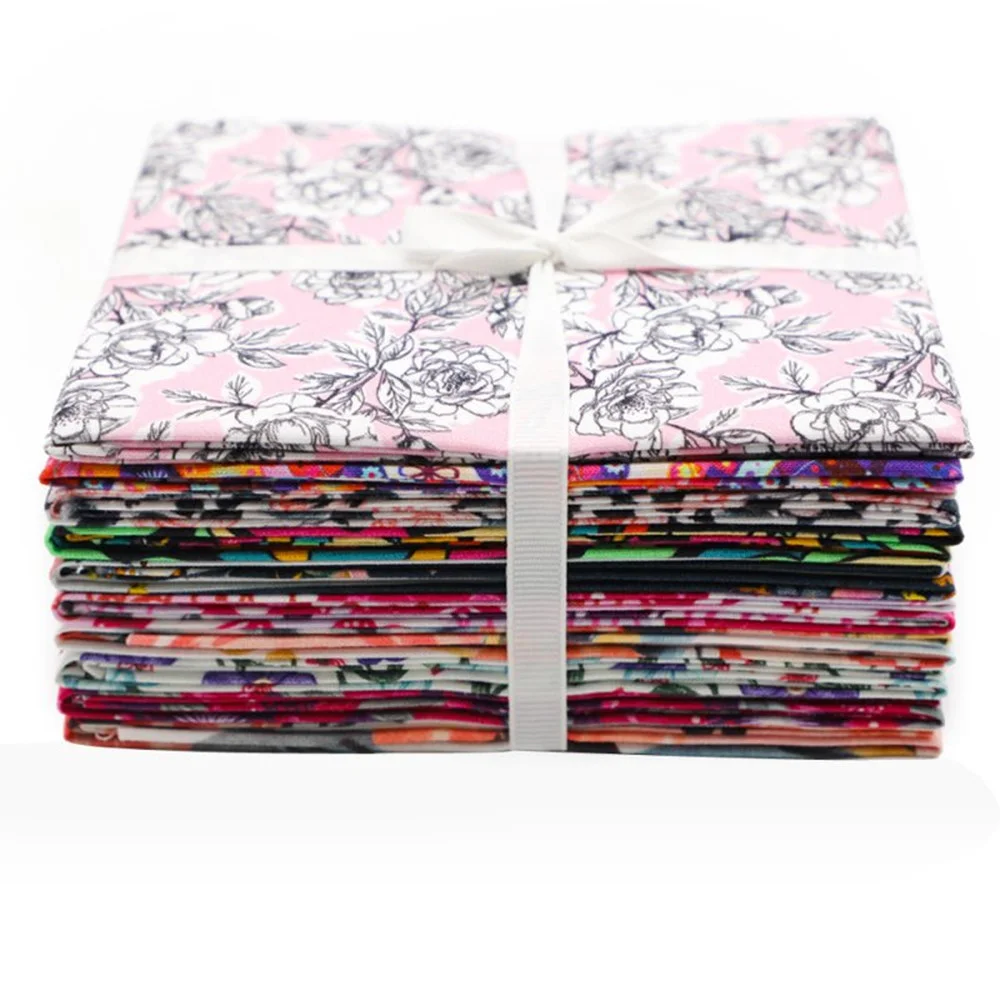

Choosing the right quilting fabric is paramount for a successful and enjoyable project, directly impacting the final quilt’s appearance, durability, and ease of construction. It’s not just about aesthetics; the fabric’s quality and characteristics play a significant role in how well it cuts, stitches, and withstands the test of time. Making informed selections at this stage ensures your creative efforts translate into a cherished, long-lasting heirloom.
This guide will walk you through the essential considerations when selecting quilting fabric, from understanding fiber content and weave to evaluating colorfastness and design compatibility. By focusing on these key aspects, you can confidently choose fabrics that will collaborate beautifully in your next quilting masterpiece, preventing common frustrations like fraying, stretching, or color bleeding down the line.
Here’s how to choose the right quilting fabric:
Fiber Content:
100% Cotton: This is the gold standard for quilting due to its stability, breathability, and ease of handling. Cotton cuts cleanly, holds its shape well, and tolerates repeated washing without excessive shrinkage or distortion, making it ideal for precise piecing.
Quality of Construction (Weave & Thread Count):
- Tight Plain Weave: Look for a fabric with a dense, tight plain weave. This construction minimizes fraying, offers excellent dimensional stability (less stretch), and ensures seams lie flat, which is critical for accurate patchwork.
- High Thread Count (60-75+ TPI): A higher thread count means more threads per inch, resulting in a smoother, more durable fabric. This density also makes the fabric easier to cut precisely and less prone to shifting during sewing.
Colorfastness & Print Quality:
- Test for Bleeding: Before extensive use, test a small swatch for colorfastness by rubbing it with a damp white cloth. This prevents vibrant colors from bleeding onto lighter fabrics, which can ruin a quilt.
- Crisp Prints & On-Grain: Examine printed fabrics for crisp, well-defined designs and ensure the print is “on-grain” (aligned with the fabric’s weave). Off-grain prints can make cutting accurately challenging and lead to a distorted finished product.
“Hand” (Feel) & Weight:
- Smooth & Substantial Hand: High-quality quilting cotton should feel smooth, soft, and substantial in your hand, not thin or flimsy. This indicates well-spun yarn and a good weave.
- Consistent Weight: Ensure all fabrics you select for a single quilt project have a similar weight. Mixing very different fabric weights can lead to uneven seams and a less cohesive quilt top.
Design & Scale:
- Variety of Scale: Choose a mix of large, medium, and small prints, along with solids or blenders, to create visual interest and balance in your quilt design. Too many large prints can overwhelm, while too many small prints can look busy.
- Color Palette Cohesion: Select fabrics that work harmoniously within your chosen color palette. Consider how colors will interact when placed next to each other, ensuring they enhance rather than clash with your overall design vision.
How Colorful Quilting Fabrics Are Produced
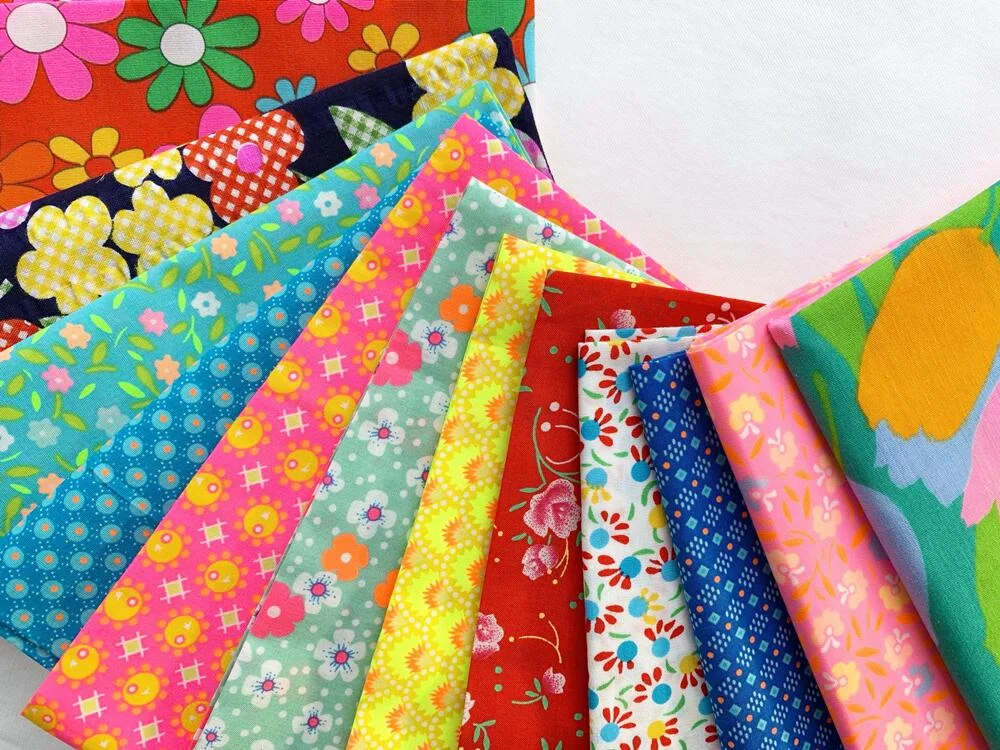
Producing the vibrant, colorfast quilting fabrics cherished by quilters involves a sophisticated interplay of chemistry and textile engineering. It begins with specially prepared cotton, which undergoes precise dyeing and printing techniques to achieve stunning, lasting hues.
The process ensures that colors penetrate deeply and designs are crisp, providing the rich palette that brings quilt designs to life while guaranteeing durability against washing and time. Each stage is crucial for the final aesthetic and performance.
Step 1: Fabric Preparation
Before any color is applied, the raw cotton fabric (greige goods) undergoes extensive preparation. This involves cleaning to remove impurities, waxes, and natural oils, often followed by a process called mercerization. This treatment physically alters the cotton fibers, making them stronger, more lustrous, and significantly enhancing their ability to absorb dyes uniformly and intensely.
Proper preparation ensures that the fabric is highly receptive to dyes and prints. It prevents blotchy or uneven coloration and maximizes the brilliance and depth of the final colors, laying the foundation for the vibrant hues seen in quilting cottons.
Step 2: Dyeing
For solid-colored quilting fabrics, large batches of prepared fabric are immersed in dye baths. Reactive dyes are commonly used for cotton because they form a strong chemical bond directly with the cellulose fibers. This covalent bond ensures exceptional colorfastness, meaning the colors won’t easily wash out or fade over time.
This method achieves deep, saturated colors that penetrate thoroughly through the fabric. The precise control of dye concentration, temperature, and time in the dye bath is critical to achieve consistent and reproducible shades batch after batch, which is important for quilters.
Step 3: Printing
For patterned quilting fabrics, designs are applied using various printing methods. Rotary screen printing is common for large-scale production, where each color in a design has a separate cylindrical screen. Dye paste is forced through the screen’s perforations onto the fabric as it passes underneath.
More intricate or custom designs might use digital textile printing, where specialized inkjet printers apply dye directly onto the fabric. Both methods allow for precise registration of colors and intricate detailing, ensuring crisp, vibrant patterns that are central to quilting fabric’s appeal.
Step 4: Steaming and Washing
After dyeing or printing, the fabric often undergoes a steaming process. The heat from the steam helps to fully “fix” the dyes onto the fibers by activating the chemical reaction between the dye and the cotton. This step is crucial for achieving permanent colorfastness.
Following steaming, the fabric is thoroughly washed. This step removes any unfixed dye particles, excess chemicals, and sizing from the fabric. Proper washing prevents colors from bleeding onto other fabrics when a quilt is laundered later, ensuring the longevity of its vibrant design.
Step 5: Finishing and Quality Control
The final stages involve various finishing treatments to enhance the fabric’s feel and performance. This can include sanforization (pre-shrinking) to minimize future shrinkage and calendering (pressing between rollers) for smoothness and a subtle sheen.
Throughout the entire process, rigorous quality control checks are performed at every stage. This ensures color consistency, print accuracy, and overall fabric quality, guaranteeing that quilters receive beautiful, reliable fabric ready for their creative projects.
Conclusion
Understanding what quilting fabric is made of reveals why it’s so essential for durable, beautiful quilts. Its composition, primarily high-quality, long-staple cotton, alongside specialized weaving and finishing, ensures stability, vibrant color, and lasting performance.
This deep dive into fiber quality, weave density, and finishing processes highlights that quilting fabric is engineered for precision and longevity. These characteristics directly contribute to the success and beauty of every stitch and seam.
For consistently high-quality materials that bring your quilting visions to life, consider sourcing wholesale quilting fabric from Fanda Fabrics.