Cotton is one of the most popular and versatile fabrics used today, found in everything from everyday clothes to high-quality quilting fabrics. But have you ever wondered how cotton goes from being a fluffy plant in the field to the soft, breathable fabric we all know and love? In this guide, we’ll walk you through the entire journey, showing you how cotton is cultivated, processed, and turned into fabric.
Understanding the process not only gives you a new appreciation for cotton but also helps you make informed choices when selecting fabrics for your next project. Whether you’re a seasoned quilter or just starting out, knowing the ins and outs of cotton manufacturing can elevate your fabric knowledge and help you select the best options for your creations.
Cotton Cultivation: Understanding the Start of the Process
Cotton cultivation is where it all starts. From seed to fabric, it’s a careful and intentional process. Let’s take a closer look at the conditions needed for healthy cotton growth, the different types of cotton, and how the plant grows, all leading to the soft, breathable fabric we love.
Ideal Growing Conditions for Cotton
Cotton plants thrive in warm climates, making them a perfect fit for tropical and subtropical regions. The soil needs to be well-drained and rich in nutrients, while the plants also require plenty of sunshine and moderate rainfall.
But beyond just climate, there are other factors that can influence the cotton’s quality. For example, pest control is vital in preventing damage, and even the local environment—like wind and soil health—can impact the final cotton yield. These small details make a big difference in the fabric we get in the end.
Cotton Varieties: A Deeper Look
Not all cotton is created the same! There are several types of cotton plants, each with unique qualities. Here are the main types of cotton, each with unique qualities:
- Gossypium hirsutum (Upland Cotton): The most common type, used in many standard cotton fabrics.
- Gossypium barbadense (Pima or Egyptian Cotton): Known for its longer, finer fibers, and used for high-quality fabrics.
- Gossypium herbaceum (Levant Cotton): Valued for its durability, often used in more rugged fabrics.
Cotton Plant Growth Stages
From seed to harvest, cotton goes through several stages. After planting, the cotton seeds germinate and sprout into seedlings. Over the growing season, the plants develop into large, bushy green plants with white blooms that eventually turn into the cotton bolls we recognize.
These bolls open up to reveal the fluffy cotton fibers. New advancements in plant genetics are helping to improve cotton’s resilience and yield, making it more sustainable and efficient to grow. This ongoing evolution means cotton plants are getting better at withstanding pests and diseases, ensuring a stronger and higher-quality product.
-
100 Cotton Solid Fabric
-
100% Cotton 10 Meters Printed Fabric Bolt
-
100% Cotton Printed Quilt Fabric Bolt
-
100% Cotton 40 Pieces 5″ Printed Green Charm Pack Quilt Fabric
-
100% Cotton Quilted Fabric 42 Pieces 5″ Printed Charms Pack
-
100% Cotton Blue Solid Color Fat Quarter
-
100% Cotton Poplin Printed Patchwork Fabrics
Harvesting: Collecting the Raw Cotton
When it comes to harvesting cotton, there are two main methods: mechanical and manual. Most cotton today is picked using machines like cotton pickers, which gently pull the fluffy cotton from the bolls, leaving the plant mostly intact.
This method is quick and efficient, especially for large fields. That said, in some regions, cotton is still picked by hand. While this method is much slower and requires a lot of manpower, it results in cleaner cotton with less debris.
After the cotton is harvested, it’s not quite ready to be spun into fabric yet. At this point, the cotton is full of debris like leaves and seeds, so it still needs a little cleaning. Whether it’s picked by hand or machine, the cotton goes through a process called ginning. This removes the seeds and other bits, preparing the cotton fibers for the next step in becoming the soft, breathable fabric we all know and love.
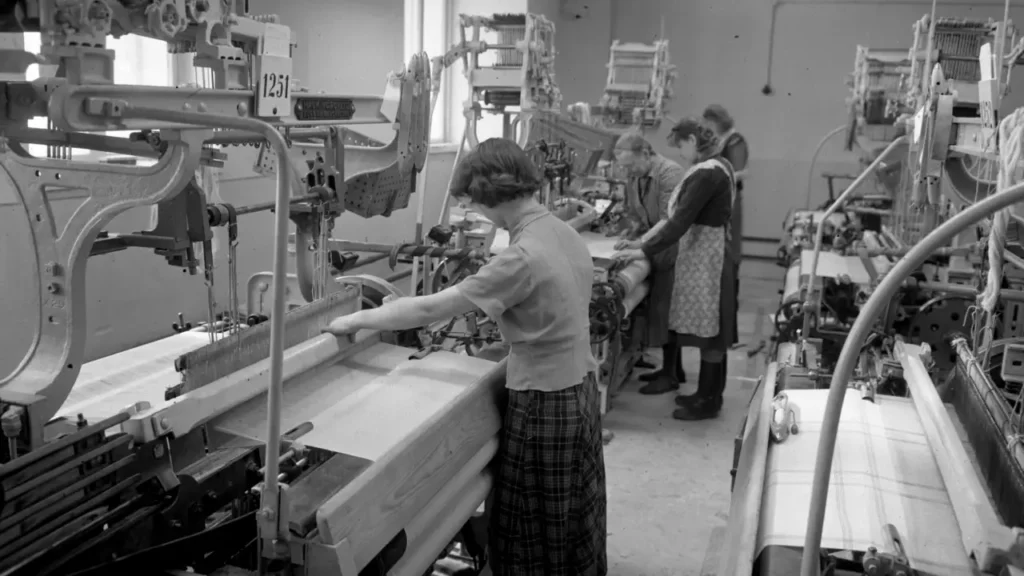
Cotton Processing: From Raw to Refined Fiber
Ginning: Separating Fiber from Seed
When cotton is picked, it’s still attached to its seeds, so the first thing that needs to happen is to get rid of them. This is where ginning comes in.
Ginning is the process that separates the soft cotton fibers from the seeds. This step is super important because the seeds don’t have a use in fabric production and would just make the fibers all tangled up. Ginning machines use rotating saws and brushes to pull the fibers free from the seeds.
Cotton Cleaning and Preparing for Spinning
Once the seeds are gone, the cotton still isn’t quite ready to spin. It needs a little cleaning to remove any leftover dirt, leaves, or bits of seeds from the ginning process. This is a key step in getting the fibers nice and smooth. The cotton goes through dusting and air-classing processes to get rid of fine particles. By the end of it, the cotton’s in tip-top shape, ready for the next phase—spinning.
Carding: The First Step to Smooth Fibers
Carding is the first big step to get cotton ready for spinning. Special machines with rotating drums and wire teeth pull the fibers apart, getting rid of any tangles or dust. This process creates a fluffy mass of fibers called a “carded sliver.” Carding is perfect for fabrics like towels or basic cotton materials, where a perfectly smooth finish isn’t needed. The goal is to get the fibers aligned and ready to spin.
Combing: Refining for High-Quality Fabrics
After carding, cotton goes through combing—a more delicate process that refines the fibers even more. While carding does a good job of straightening the fibers, combing takes it a step further by removing the short, weak fibers that could make the fabric feel rough.
The fibers are brushed and aligned to make them super smooth and even. Combing is essential for high-end fabrics like Pima or Egyptian cotton, where softness and strength are key. If you’re making something soft like bed linens or a luxurious quilt, combing helps give it that extra smoothness and durability.
Spinning: Creating Yarn from Cotton Fibers
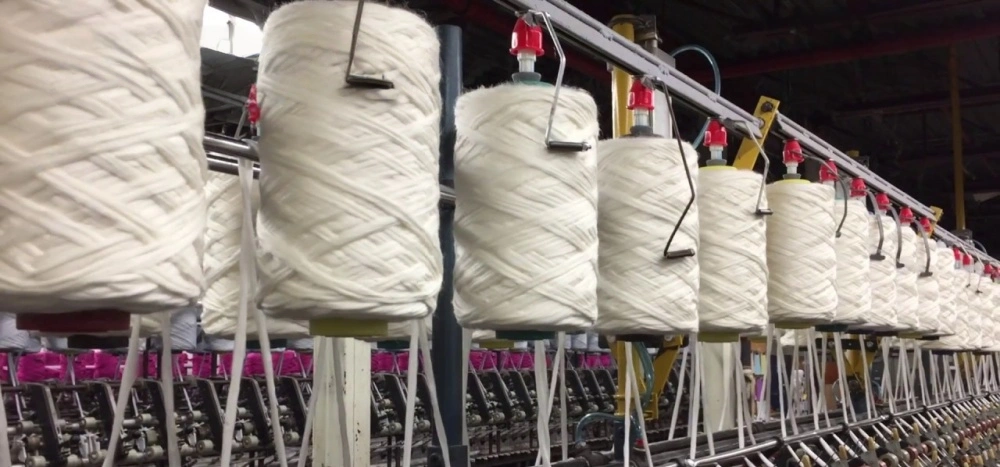
From Fiber to Yarn
Once the cotton fibers are cleaned, straightened, and aligned, they’re ready to be spun into yarn. This is where the magic happens! Spinning machines twist the fibers together, creating long, continuous strands of yarn.
This yarn is then ready to be woven or knitted into fabric. Depending on how tightly the fibers are twisted, the yarn can vary in thickness and texture. This is a crucial step because it determines how soft, durable, and overall cozy the fabric will feel in the end.
Different Types of Yarn
Types of Yarn:
- Fine yarns: Soft and smooth, ideal for lightweight, delicate fabrics.
- Coarse yarns: Thicker and rougher, perfect for durable, heavier materials.
Spinning Methods:
- Open-end spun: Quicker to produce, bulkier, and has a more textured feel.
- Ring-spun: The fibers are twisted tightly, creating a smoother, stronger yarn.
Weaving and Knitting: Turning Yarn into Fabric
Weaving Process
Weaving is all about crossing threads to make fabric. You’ve got two main elements here: the warp (the vertical thread) and the weft (the horizontal thread that goes in and out). It all starts with setting up these threads on a loom—a machine that weaves them together into fabric.
Here’s how the process works:
Warping: This is when the long threads (the warp) are wound onto beams to get them ready for weaving.
Sizing: The warp threads get a special coating to make them stronger and easier to work with.
Weaving: Now comes the fun part, where the threads are woven together using the loom. There are different techniques that give the fabric unique looks:
- Satin: A smooth and shiny finish, found in luxe fabrics like satin and charmeuse.
- Plain Weave: The most basic weave, where the threads alternate for a balanced fabric.
- Twill: This creates a diagonal pattern, often seen in denim or khakis.
Knitting Process
Knitting is a whole other ballgame. Instead of weaving threads together, knitting uses yarn to create loops that lock together, making fabric that’s stretchy and comfy. Think about your favorite cotton sweater or T-shirt—that’s knitted cotton!
Here are the main types of knitted fabrics:
- Jersey: This smooth fabric is made with a single set of loops, and it’s great for casual pieces like t-shirts.
- Interlock: A thicker knit that’s double-sided, perfect for more structured clothes.
Fabric Finishing: Enhancing Texture and Durability
Types of Finishing Techniques
Mechanical Finishing
Mechanical finishing uses machines to change the fabric physically. Some of the most common methods are:
- Calendering: This technique presses fabric with heated rollers to make it smoother and shinier. Think of it as giving your fabric a sleek, polished look. It’s often used for things like bedding or dress fabrics.
- Mercerizing: This process treats fabric with a special solution to give it a smooth, glossy finish. It also strengthens the fabric, making it more durable and resistant to shrinking. Mercerized cotton feels silkier and looks extra shiny.
- Singeing: Singeing burns off those stray fibers that stick out, leaving the fabric smooth and clean. It’s like tidying up the fabric’s edges to make it perfect.
Chemical Finishing
Chemical finishing involves using chemicals to enhance the fabric. Some common techniques include:
- Dyeing: Dyeing adds color to fabric, turning it from plain to vibrant. It can be done in a variety of ways—solid color or multi-color patterns, depending on the look you want.
- Printing: Similar to dyeing but with more creative freedom. Printing allows you to add specific designs or patterns to the fabric, like those cute floral prints on dresses or fun designs on kids’ pajamas.
- Water Repellent Finishes: Water-resistant finishes are applied to fabrics that need a bit of protection from the elements. These finishes help keep moisture out, making them perfect for outdoor gear or rain jackets.
Eco-Friendly Finishing Technologies
With environmental awareness on the rise, the textile industry has come up with some eco-friendly finishing methods. These include:
- Non-Toxic and Biodegradable Finishes: More eco-conscious finishes are popping up, free from harmful chemicals and able to break down naturally, leaving no harmful residues behind.
- Low-Impact Dyeing: This method uses less water and energy, so it’s better for the planet while still giving your fabric vibrant color.
Post-Finishing Quality Control
After your fabric gets its finishing touches, it’s time for a quick check to make sure everything is up to snuff. This quality control ensures your fabric stays consistent and top-notch.
- Testing for Colorfastness: This test checks how well the fabric holds its color after washing. It’s important for fabrics that will be washed frequently—like your favorite pair of jeans or that cotton shirt you wear all the time.
- Testing for Shrinkage: No one wants fabric that shrinks after the first wash! Shrinkage testing ensures the fabric won’t shrink too much once it’s washed, keeping it the perfect size.
- Testing for Strength: This test checks if the fabric is durable enough to stand up to wear and tear. Whether it’s a pair of pants or a bedsheet, you want your fabric to last.
Fabric Inspection
To make sure everything’s just right, fabric inspection is done. This process checks for any defects or inconsistencies in texture, color, and strength. It guarantees that each piece of fabric meets the same high standard, so your cotton fabrics always look and feel great.
Sustainability in Cotton Manufacturing
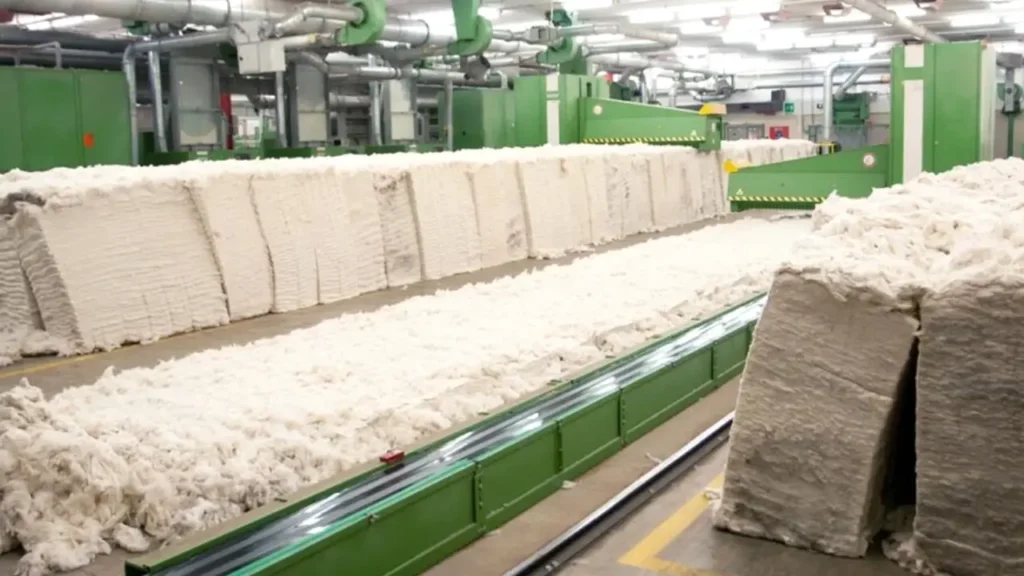
When you think of cotton, you probably picture your favorite pair of pajamas or those soft, cozy sheets you can’t get enough of. But did you know that the way cotton is produced can have a huge impact on the planet?
As we become more eco-conscious, the cotton industry is evolving, and there’s a lot happening to make cotton farming and manufacturing greener. Let’s dive in and see how things are changing for the better!
Eco-Friendly Cotton Production
Organic Cotton
Organic cotton is a total game-changer. Unlike conventional cotton, it’s grown without harmful fertilizers or pesticides, which not only protects the environment but also helps the farmers who grow it. Organic farms use crop rotation and natural fertilizers, reducing the need for extra water and chemicals. It’s a win for both your clothes and the planet!
Water Conservation
Cotton farming has a reputation for being water-intensive, but that’s changing. Farmers today are using smart techniques like drip irrigation to deliver water straight to the roots, reducing waste. Some farms even collect rainwater and reuse it during dry spells, helping save water and making cotton farming a lot more sustainable.
Recycled Cotton
Waste is a big issue in textiles, but recycled cotton is here to help. By reusing cotton fibers from old clothes or leftover fabric, we reduce the need to grow new cotton. This not only cuts down on waste but also saves valuable resources like water and energy. So when you buy recycled cotton products, you’re doing your part to reduce waste and support a greener future.
Certified Cotton and Fair Trade
Understanding Cotton Certifications
Ever noticed labels like GOTS (Global Organic Textile Standard) or Fair Trade on your cotton products? These are certifications that tell you the cotton was grown sustainably and under fair working conditions.
GOTS means the cotton is organic, and Fair Trade ensures that farmers get paid fairly for their hard work. These certifications give you peace of mind that your purchase is both eco-friendly and socially responsible.
Traceability and Transparency
More people are curious about where their cotton comes from and how it’s produced. That’s where traceability and transparency come in. When brands provide this info, you can see exactly where and how the cotton is sourced.
This means you can shop confidently, knowing your cotton is ethically produced and has a minimal impact on the environment. It’s a simple way to make sure your purchases are part of the solution.
Circular Economy in Cotton Fabric
The circular economy is all about reducing waste and reusing what we already have. In the cotton industry, this means recycling fabrics at the end of their life, instead of tossing them away. By giving old cotton fabrics a second life, we can reduce the need for new cotton, minimize landfill waste, and create a more sustainable system. The more we embrace this, the better it is for the planet.
Conclusion
From the fields where cotton is picked to the fabric that ends up in your quilt, every step plays a part in making the soft, breathable textiles we all love. Cotton continues to be a favorite for everything—from comfy clothes to cozy home textiles—because it’s comfortable, durable, and versatile. No wonder this natural fiber has stood the test of time!
Next time you’re shopping for quilting fabric, why not make a sustainable choice? Go for high-quality, eco-friendly cotton quilting fabrics from F&A Fabric. By choosing organic or recycled cotton, you’ll support a greener, more responsible industry and create beautiful projects you can feel proud of. Happy quilting!