Calico fabric, with its simple, unbleached appearance, has a long and storied history. But have you ever wondered how this versatile fabric is actually made? This blog post will delve into the fascinating process of calico fabric manufacturing, from the cultivation of cotton to the final stages of production. We’ll explore the key steps involved, including ginning, carding, spinning, weaving, and finishing, providing you with a deeper understanding of how this everyday material comes to life.
Whether you’re a seasoned textile enthusiast or simply curious about the journey of your favorite fabrics, this post will offer a glimpse into the world of calico production and the skilled craftsmanship that goes into creating this timeless material.
What Is Calico Fabric
Calico is a type of plain-woven cotton fabric. It’s known for its simple, even weave and its natural, unbleached color, which can range from creamy white to off-white. Traditionally, calico was inexpensive and widely used for everyday items due to its affordability and durability.
Today, calico remains a popular choice for various purposes. It’s often used in quilting and patchwork projects, as well as for creating home decor items like curtains, tablecloths, and bags. Some people also use it for dyeing, painting, and printing, allowing for unique and personalized creations.
What Is Calico Fabric Made from
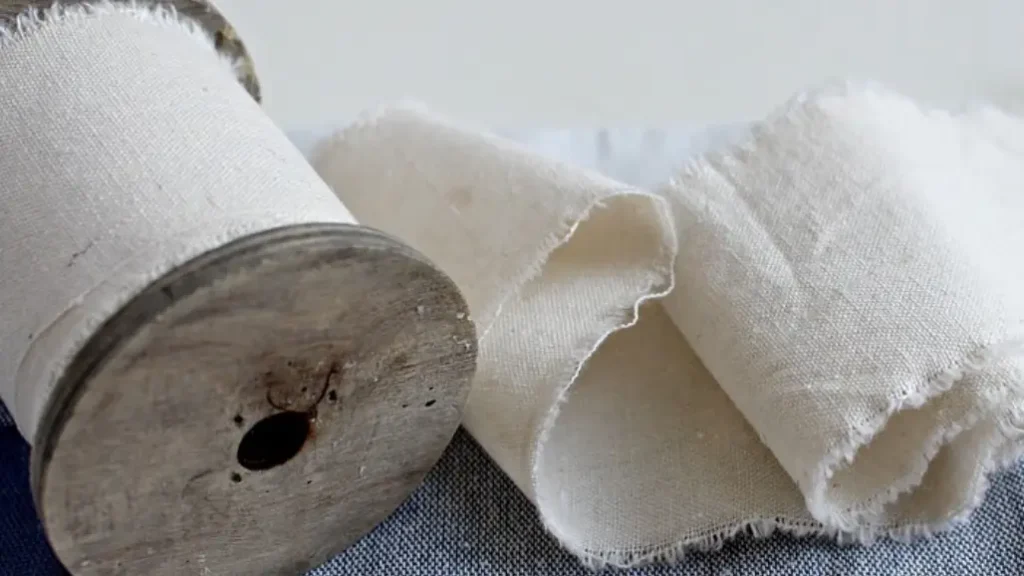
Calico fabric is primarily made from cotton.
- Cotton: This natural fiber is grown from the cotton plant and is known for its softness, breathability, and durability.
Calico is typically made from 100% cotton, although there might be some variations or blends with other natural fibers in some cases.
How is Calico Fabric Made
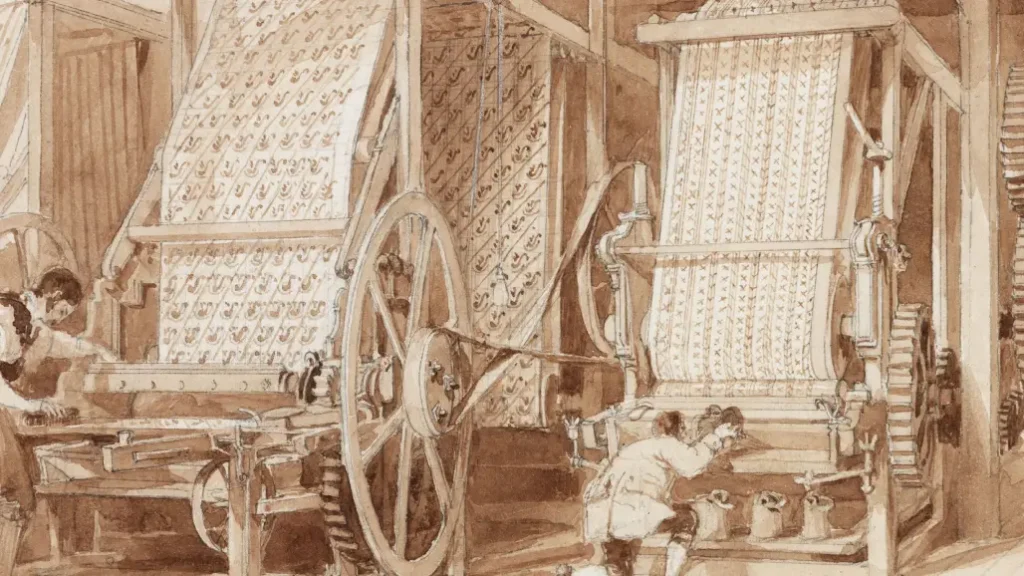
Calico is a type of plain-woven cotton fabric renowned for its simple, even weave and its natural, unbleached color, which ranges from creamy white to off-white. Its production involves a multi-step process, beginning with the cultivation and harvesting of cotton.
The harvested cotton undergoes ginning to separate the fibers from the seeds, followed by cleaning and conditioning to prepare the fibers for spinning. The spun yarn is then woven into fabric using a plain weave.
Finally, the woven fabric undergoes finishing processes such as washing, bleaching, and drying, followed by inspection and packaging before reaching the market.
Step 1: Cotton Cultivation and Harvesting
Cotton cultivation begins with planting seeds in fertile soil. These plants thrive in warm climates with ample sunlight. Farmers meticulously care for the crops, ensuring proper irrigation, fertilization, and weed control. Once the cotton bolls mature, they burst open, revealing the fluffy white fibers within. Harvesting can be done manually, often by hand-picking, or mechanically using specialized machines that efficiently extract the cotton bolls from the plants.
Step 2: Ginning
Ginning is a critical step in the cotton processing journey. Its primary function is to separate the cotton fibers from the seeds. Traditionally, this was a labor-intensive process, but the invention of the cotton gin revolutionized the industry. Modern ginning machines utilize a combination of rollers and saws to effectively remove the seeds from the cotton. This process is crucial as the seeds can significantly hinder the subsequent steps in fabric production.
Step 3: Cleaning and Conditioning
The raw cotton fibers obtained after ginning contain various impurities such as leaves, twigs, dirt, and even small pieces of seed hulls. These impurities can adversely affect the quality of the final fabric. The cleaning process involves meticulously removing these foreign materials using specialized machinery. This may include processes like air cleaning, where air currents are used to separate lighter impurities from the heavier cotton fibers.
Following cleaning, the cotton fibers undergo conditioning. This stage aims to prepare the fibers for the spinning process. Conditioning typically involves several steps, including blending different types of cotton to achieve desired qualities like strength and softness. Carding is another crucial step where the fibers are aligned and disentangled, creating a more uniform and consistent cotton mass. Combing, a more refined process, further refines the fibers, removing any remaining short fibers and impurities.
Step 4: Spinning
Spinning transforms the prepared cotton fibers into yarn, the fundamental building block of fabric. This involves twisting the fibers together to create a continuous thread. The spinning process can vary depending on the desired yarn characteristics, such as thickness, strength, and evenness.
There are various spinning methods, including ring spinning, which is a widely used technique. In ring spinning, the fibers are drawn through a series of rollers, gradually twisting them into a yarn. The yarn is then wound onto bobbins for subsequent use in weaving. The spinning process is crucial as the quality of the yarn directly impacts the final fabric’s strength, durability, and appearance.
Step 5: Weaving
Weaving is the process of interlacing the spun yarns to create fabric. In the case of calico, a plain weave is employed. This is the simplest and most common weave structure, where the warp yarns (running lengthwise) and weft yarns (running crosswise) interlace in a straightforward over-under pattern.
The weaving process takes place on a loom, a machine that holds and guides the yarns during the weaving process. The warp yarns are held taut on the loom, while the weft yarns are inserted across the warp yarns using a shuttle or other mechanisms. The interlacing of the yarns creates the fabric structure, determining its strength, drape, and overall appearance.
Step 6: Finishing
Once the fabric is woven, it undergoes a finishing process to prepare it for use. This typically includes washing to remove any residual impurities, such as sizing agents or lubricants, that were applied during the weaving process.
Bleaching is often performed to achieve the characteristic off-white color of calico. This involves treating the fabric with chemicals to remove natural pigments and achieve a bright, uniform appearance. The fabric is then thoroughly rinsed to remove any remaining chemicals.
Drying is another essential step in the finishing process. The fabric is typically dried in large drying machines, ensuring even and efficient moisture removal. The drying process also helps to set the fabric’s dimensions and prepare it for subsequent processes, such as dyeing or printing.
Step 7: Inspection and Packaging
Before the finished calico fabric reaches the market, it undergoes rigorous inspection to ensure quality and identify any defects. This may involve visual inspection for flaws like tears, holes, or unevenness in the weave.
Once the fabric passes inspection, it is carefully packaged for transportation and distribution. Packaging methods may vary depending on the quantity and type of fabric. The fabric may be folded, rolled, or baled to protect it during transport.
This calico fabric manufacturing process highlights the intricate journey of calico fabric production, from the cultivation of cotton to the final packaging of the finished product. Each step plays a crucial role in determining the quality and characteristics of the final fabric.
Is Calico the Same as Raw Cotton?
No, calico and raw cotton are not the same.
Raw cotton refers to the cotton fibers as they are harvested from the plant. It’s essentially the unprocessed material, still containing impurities like seeds, leaves, and dirt.
Calico, on the other hand, is a type of woven fabric made from cotton. It has undergone several stages of processing, including ginning (separating the fibers from the seeds), cleaning, spinning the fibers into yarn, and finally weaving the yarn into fabric. Calico is typically unbleached, giving it a natural, off-white color.
Therefore, raw cotton is the starting material, while calico is the finished product after a series of manufacturing processes.
Is Calico Fabric Expensive?
Calico fabric is generally considered to be an affordable option.
It’s typically made from plain-woven cotton, which is a relatively inexpensive natural fiber. The simple production process, involving a basic weave and often minimal embellishments, also contributes to its affordability.
Of course, the price can vary depending on factors such as the specific brand, the quality of the cotton, any added designs or prints, and where you purchase the fabric. However, compared to many other types of cotton fabric, calico is usually a budget-friendly choice for various sewing and crafting projects.
Conclusion
In conclusion, calico fabric is a versatile and enduring textile with a rich history. Its simple production process, involving primarily cotton and a plain weave, makes it an affordable and accessible material. Whether used for everyday items or creative projects, calico continues to be a popular choice for its practicality, durability, and potential for customization.
Ready to bring your calico fabric ideas to life? FandaFabrics.com is your one-stop shop for high-quality wholesale calico fabric. With a wide variety of colors and patterns to choose from, you’re sure to find the perfect fabric for your next project. Plus, our wholesale prices ensure you get the best value for your money.
So don’t wait any longer! Visit FandaFabrics.com today and start browsing our selection of calico fabric. We can’t wait to help you create something beautiful!