Fabric finishes are crucial in enhancing a textile’s performance and aesthetic. This guide delves into the diverse world of fabric finishes, exploring their types, benefits, and applications. From water resistance to wrinkle-free properties, these treatments transform raw fabric into functional and appealing materials. Understanding fabric finishes empowers you to make informed choices for various projects.
This comprehensive guide covers everything from basic finishes like calendaring to advanced treatments like antimicrobial coatings. We’ll explore how these finishes impact fabric properties, durability, and suitability for different uses. Whether you’re a designer, crafter, or manufacturer, this guide provides valuable insights into maximizing fabric potential.
What Is Fabric Finish
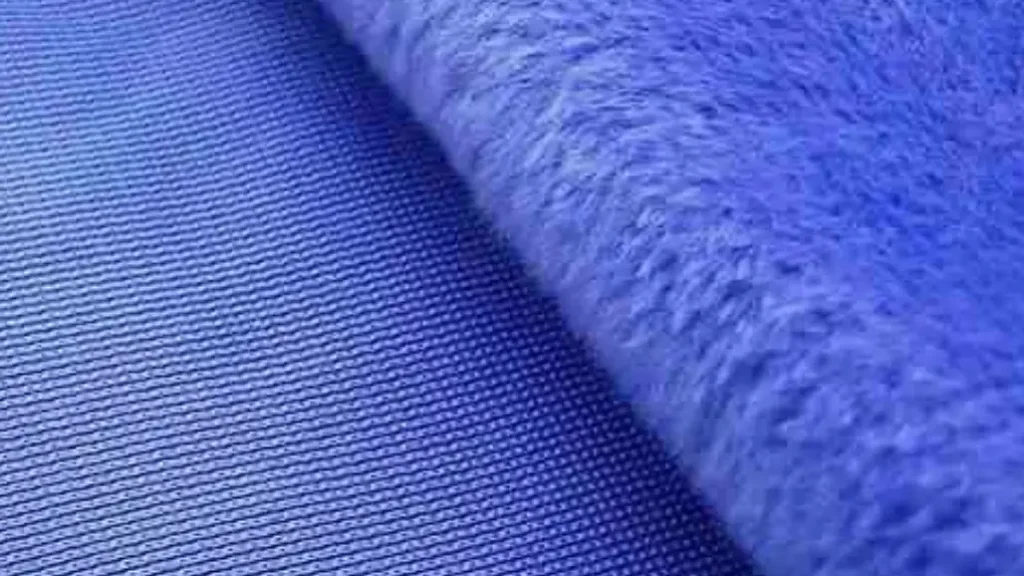
Fabric finish refers to the processes applied to textiles after they have been woven or knitted, aimed at enhancing their performance, appearance, or feel. These treatments modify the fabric’s properties, making it more suitable for specific applications. Finishes can range from simple processes like calendaring, which smooths the fabric, to more complex chemical treatments that impart water resistance, flame retardancy, or wrinkle resistance.
The purpose of a fabric finish is to improve the fabric’s usability and longevity. It can alter the fabric’s texture, making it softer or stiffer, or add protective qualities, such as UV protection or antimicrobial properties. Different finishes cater to diverse needs, from enhancing the drape and luster of apparel fabrics to improving the durability and functionality of industrial textiles. Understanding fabric finishes is crucial for selecting the right material for any given project.
Fabric Finishes Types
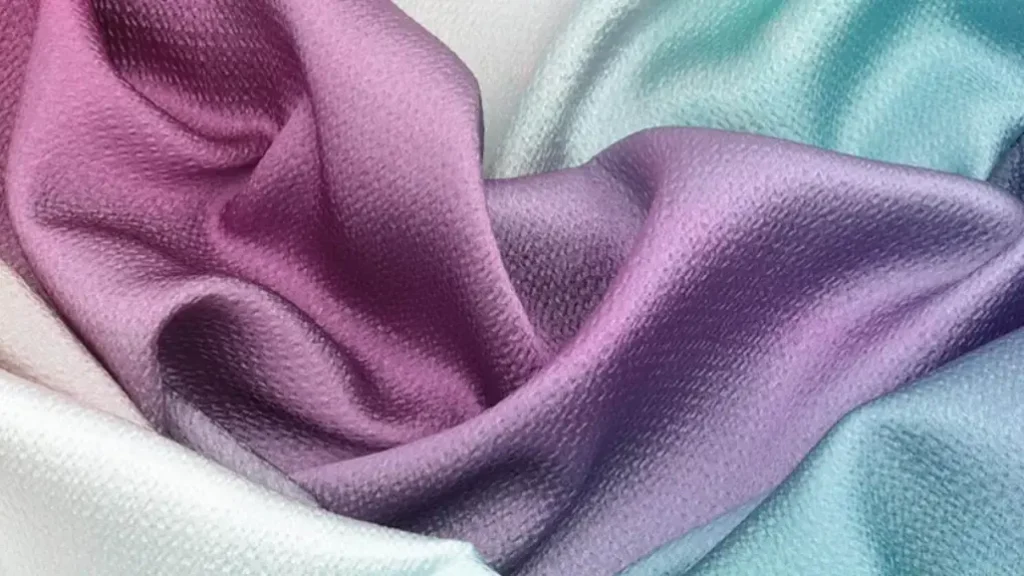
Fabric finishes are crucial in tailoring textiles for specific uses, enhancing their properties from aesthetics to functionality. These treatments transform raw materials into versatile fabrics, meeting diverse consumer demands. Understanding the various types of fabric finishes allows for informed choices in textile selection.
1. Mechanical Fabric Finishes
Mechanical fabric finishes alter fabric surfaces through physical manipulation, without chemical applications. Calendering, using heated rollers, smooths or embosses fabrics, changing their texture and luster. Raising, a brushing technique, creates a nap, enhancing warmth and softness. These processes focus on physical alterations, impacting the fabric’s tactile and visual qualities. For instance, calendaring can impart a glossy sheen to fabrics, while raising creates a plush, fuzzy surface. Mechanical finishes are often used to enhance the aesthetic appeal and comfort of textiles, making them more desirable for specific applications.
2. Chemical Fabric Finishes
Chemical fabric finishes involve the application of substances to modify fabric properties, such as water repellency, flame retardancy, or wrinkle resistance. These treatments enhance durability and performance by altering the fabric’s chemical composition. Chemical finishes provide functional improvements, making fabrics suitable for specific environments and applications. For example, water-repellent finishes apply hydrophobic substances, causing water to bead and roll off. Flame-retardant finishes use chemicals to inhibit combustion, enhancing safety. These treatments are essential for creating specialized textiles for various industries.
3. Thermal Fabric Finishes
Thermal fabric finishes use controlled heat to set or modify fabric structures. Heat setting stabilizes synthetic fibers, preventing shrinkage and maintaining shape. Singeing removes surface fibers, creating a smooth finish and preventing pilling. These processes use heat to alter the fabric’s physical structure, ensuring stability and improved surface characteristics. For instance, heat setting is crucial for polyester fabrics, preventing them from shrinking during washing. Singeing is often used on cotton fabrics to remove fuzz and create a clean, smooth surface, enhancing their appearance and durability.
4. Aesthetic Fabric Finishes
Aesthetic fabric finishes enhance visual appeal through dyeing, printing, and embossing. Dyeing adds color, printing adds patterns, and embossing adds texture, transforming plain fabrics into visually appealing textiles. These techniques improve the fabric’s appearance, making it more attractive for various applications. Aesthetic finishes focus on visual enhancements, providing diverse design options. For example, dyeing can create vibrant, uniform colors, while printing allows for intricate patterns and designs. Embossing adds depth and texture, creating unique visual effects.
5. Performance Fabric Finishes
Performance fabric finishes enhance functional properties like antimicrobial treatments, UV protection, and stain resistance. These treatments improve usability and longevity in specific environments. Antimicrobial finishes prevent microbial growth, reducing odors and enhancing hygiene. UV protection prevents sun damage, extending the fabric’s lifespan. Stain resistance prevents stains, simplifying care. These finishes are essential for creating textiles that meet specific performance requirements, such as those used in healthcare, sports apparel, and outdoor gear.
6. Durable Press Fabric Finishes
Durable press fabric finishes reduce wrinkling and maintain a smooth appearance after washing. Chemical resins crosslink fibers, ensuring shape retention and minimal ironing. These treatments simplify garment care, providing a neat appearance with reduced maintenance. Durable press finishes are essential for creating garments that require minimal upkeep, such as business attire and uniforms. These treatments ensure a professional look with minimal effort, saving time and effort on ironing and garment care.
7. Water Repellent Fabric Finishes
Water repellent fabric finishes resist water penetration by applying hydrophobic substances to the fabric surface. These treatments cause water to bead and roll off, protecting the fabric from moisture. Water-repellent finishes enhance the fabric’s ability to shed water, making it suitable for outdoor and protective clothing. These finishes are crucial for creating textiles that can withstand wet conditions, such as raincoats, tents, and outdoor gear. They ensure that the fabric remains dry and comfortable, even in heavy rain.
8. Flame Retardant Fabric Finishes
Flame retardant fabric finishes reduce flammability by applying chemicals that inhibit combustion. These treatments enhance safety in applications with fire hazards. Flame-retardant finishes slow down or prevent the spread of flames, providing crucial protection in environments where fire safety is a concern. These finishes are essential for creating textiles used in public spaces, such as theaters and hospitals, as well as for protective clothing used by firefighters and industrial workers. They reduce the risk of fire-related injuries and damage.
9. Antimicrobial Fabric Finishes
Antimicrobial fabric finishes inhibit bacteria and fungi growth, reducing odors and enhancing hygiene. These treatments apply substances preventing microbial proliferation. Antimicrobial finishes are essential for healthcare and sports apparel, ensuring cleanliness and reducing the risk of infections and unpleasant odors. These finishes are crucial for creating textiles that come into close contact with the skin, such as medical textiles, athletic wear, and bedding. They help to maintain a hygienic environment and prevent the spread of harmful microorganisms.
10. Softening Fabric Finishes
Softening fabric finishes improve the fabric’s hand feel through chemical softeners or mechanical processes. These treatments make the fabric softer and more comfortable to wear. Softening finishes enhance comfort and drape, making fabrics more pleasant to the touch and suitable for intimate apparel and bedding. These finishes are essential for creating textiles that are worn close to the skin, such as undergarments, pajamas, and baby clothes. They enhance the fabric’s comfort and softness, making it more enjoyable to wear.
11. Stiffening Fabric Finishes
Stiffening fabric finishes add rigidity with resins or other substances, suitable for interlinings and structured garments. These treatments increase the fabric’s stiffness, providing structure and support. Stiffening finishes are crucial for creating garments that maintain their shape and integrity, such as tailored clothing and accessories. They are used in applications where a firm, structured appearance is desired, such as in collars, cuffs, and hat brims.
12. Wrinkle Resistant Fabric Finishes
Wrinkle resistant fabric finishes minimize wrinkling with resins that crosslink fibers, maintaining a smooth appearance. These treatments reduce the fabric’s tendency to crease, simplifying garment care. Wrinkle-resistant finishes are essential for creating garments that require minimal ironing, such as travel clothing and professional attire. They ensure a polished look with minimal effort, saving time and effort on garment maintenance.
13. Mercerizing Fabric Finishes
Mercerizing fabric finishes improve cotton luster and strength with a sodium hydroxide solution. This treatment enhances dye uptake and sheen, enhancing the fabric’s appearance and durability. Mercerizing finishes are particularly beneficial for high-quality cotton textiles, such as those used in fine shirts and bedding. They create a smooth, lustrous surface and improve the fabric’s ability to absorb dyes, resulting in vibrant, long-lasting colors.
14. Napping Fabric Finishes
Napping fabric finishes create a raised, fuzzy surface by brushing the fabric. This process raises fibers, enhancing warmth and softness, commonly used in fleece and flannel. Napping finishes improve thermal insulation and comfort, making fabrics ideal for cold-weather clothing and blankets. They create a soft, plush surface that traps air, providing warmth and comfort in cold environments.
15. Sanforizing Fabric Finishes
Sanforizing fabric finishes pre-shrink cotton fabrics by compressing them. This process reduces shrinkage during washing, ensuring garment size and shape retention. Sanforizing finishes prevent garments from shrinking after washing, ensuring a consistent fit and extending their lifespan. They are essential for creating cotton garments that maintain their size and shape, even after repeated washings, providing a reliable and consistent fit.
16. Calendering Fabric Finishes (Embossing Variant)
Calendering, when used for embossing, creates raised designs or patterns on the fabric’s surface. This mechanical finish employs heated rollers with engraved patterns, pressing the design into the textile. Embossing adds a three-dimensional texture, enhancing the fabric’s aesthetic appeal and tactile quality. This finish is often used for decorative fabrics, such as those used in upholstery, drapery, and fashion. Embossing can create intricate designs, from floral patterns to geometric shapes, adding depth and visual interest. It transforms plain fabrics into luxurious textiles, suitable for high-end applications.
17. Beetling Fabric Finishes
Beetling is a mechanical finish primarily used on linen fabrics to flatten and impart a lustrous sheen. The fabric is pounded with wooden hammers or mallets, flattening the yarn and closing the weave. This process enhances the linen’s smoothness and reflectivity, creating a characteristic glossy appearance. Beetling also increases the fabric’s density and durability, making it more resistant to wear and tear. This finish is traditionally used on linen for tablecloths, napkins, and other fine household textiles. Beetling imparts a unique, refined look, enhancing the fabric’s elegance and longevity.
18. Moire Fabric Finishes
Moire finishes create a wavy, watermarked pattern on fabrics, particularly those with a ribbed weave. This effect is achieved by calendering two layers of ribbed fabric together, causing the ribs to flatten and create an irregular pattern. The moire effect is unique and unpredictable, resulting in a shimmering, iridescent appearance. This finish is often used on silk, rayon, and acetate fabrics for formal wear, drapery, and upholstery. Moire adds a luxurious, sophisticated touch to textiles, making them visually striking and elegant. The pattern varies depending on the fabric’s weave and the calendering process.
19. Fulling Fabric Finishes
Fulling is a process used primarily on woolen fabrics to shrink and thicken them, creating a dense, felted texture. This mechanical finish involves immersing the fabric in water and subjecting it to heat and pressure, causing the fibers to interlock. Fulling enhances the fabric’s warmth, durability, and water resistance, making it suitable for outerwear, blankets, and upholstery. This process is crucial for creating felted wool fabrics, which are known for their exceptional warmth and insulating properties. Fulling transforms loosely woven wool into a compact, robust textile, enhancing its performance and longevity.
20. Glazing Fabric Finishes
Glazing applies a smooth, glossy finish to fabrics, enhancing their luster and creating a polished appearance. This finish involves applying a resin or wax coating to the fabric’s surface and then calendering it with heated rollers. Glazing enhances the fabric’s sheen and provides a degree of water resistance, making it suitable for outerwear, linings, and decorative textiles. This finish is often used on cotton and synthetic fabrics to create a smooth, shiny surface. Glazing adds a refined, polished look, enhancing the fabric’s visual appeal and protective qualities.
How to Choose the Right Fabric Finishes
Choosing the right fabric finishes is crucial for ensuring your textiles meet specific performance and aesthetic requirements. Begin by clearly defining the intended use of the fabric. Consider the environment in which it will be used, the level of durability required, and any specific functional needs, such as water resistance, flame retardancy, or antimicrobial properties.
For instance, outdoor fabrics need UV protection and water repellency, while children’s clothing benefits from flame retardancy and antimicrobial finishes. Understanding these needs will guide you toward the appropriate finish types.
Next, evaluate the fabric’s base material and its compatibility with various finishes. Different fibers react differently to chemical and mechanical treatments. Cotton, for example, is well-suited for mercerizing and durable press finishes, while synthetic fibers often benefit from heat setting and water-repellent coatings. Consider the fabric’s weave and weight, as these factors also influence the effectiveness of finishes. For example, tightly woven fabrics may require different treatments than loosely woven ones. Additionally, assess the long-term impact of the finish on the fabric’s lifespan and maintenance requirements.
Finally, consider the aesthetic qualities you wish to achieve. Finishes can significantly alter a fabric’s appearance, texture, and feel. Decide whether you need a glossy or matte finish, a soft or stiff hand, or a specific pattern or texture. Evaluate the environmental impact of the finishes, opting for sustainable and eco-friendly options when possible. Here are key considerations:
- Manufacturer Recommendations: Seek expert advice from manufacturers, ensuring informed choices based on technical expertise and experience.
- Intended Use: Define the fabric’s purpose and environment, ensuring finishes meet functional needs like water resistance or flame retardancy.
- Base Material Compatibility: Match finishes to the fiber type, as different fibers respond uniquely to chemical and mechanical treatments.
- Weave and Weight: Consider fabric structure, as weave and weight influence finish effectiveness, impacting durability and performance.
- Durability Needs: Assess the fabric’s exposure to wear and tear, ensuring finishes enhance longevity for specific applications.
- Aesthetic Goals: Choose finishes that achieve desired appearance, texture, and feel, aligning with the project’s visual requirements.
- Maintenance Requirements: Understand care instructions, ensuring finishes align with practical maintenance and cleaning needs.
- Environmental Impact: Opt for sustainable and eco-friendly finishes, minimizing environmental footprint and promoting responsible choices.
- Cost Considerations: Balance finish performance with budget, ensuring cost-effectiveness without compromising essential functionalities.
- Testing and Sampling: Verify finish effectiveness through testing, ensuring desired performance and quality before full-scale production.
Conclusion
Understanding fabric finishes is essential for maximizing fabric performance and aesthetics. From water resistance to wrinkle-free properties, these treatments enhance durability and functionality. Whether you’re a designer, manufacturer, or DIY enthusiast, choosing the right finish ensures your textiles meet specific needs. This guide provides a comprehensive overview, empowering you to make informed decisions for your projects.
Fabric finishes transform raw textiles into versatile materials, catering to diverse applications. By selecting appropriate treatments, you can tailor fabrics for optimal performance in various environments. This knowledge enables you to create products that not only look good but also withstand the test of time and use.
For premium quality, customizable wholesale fabrics, including specialized finishes, contact Fanda Fabrics. We offer a wide range of options to meet your specific requirements. Get a quote today and experience the difference in quality and service.